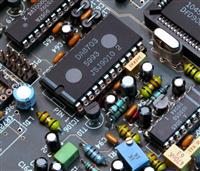
Flex PCB, or FPC for short, is a patterned arrangement of printed circuits and components that make use of flexible base material with or without a flexible cover layer. It can be bent, wound, folded freely, and withstand millions of dynamic bending without damaging the wire.
Figure 1: Flex PCB manufactured by PCBgogo
Flex PCB offers freedom of design, making it possible to fit the desired applicable shape and move or expand in three-dimensional space. The compact nature and high electrical-connection density of Flex PCB offer us lighter weight and smaller space compared to the traditional rigid PCB. Its advantages can be summarized as follows:
Bendable and and flexible
Small size and lightweight
High circuit density
High reliability
Applications of Flex PCB
First developed in the 1960s, Flex PCB was initially used in high-precision electronic products such as aerospace and military. After the end of the Cold War, it began to be applied in civilian products. Entering the 21st century, the application of Flex PCB has been fully expanded driven by the development of Flex PCB technology and the trend of lightness and thinness of the final products.
As the electronics products bring greater functionality while coming in smaller and lighter sizes, the need for Flex PCB has grown immensely. The qualities of Flex PCB meet the trend of multifunctional, miniaturized, and portable electronics. Therefore, it is widely used in PC and peripheral products, automotive electronics, medical equipment, communication products, consumer electronics, and other fields. In this article, we will discuss the applications of Flex PCB especially in smartphones, wearable devices, and the automotive electronics industry.
1. Smartphones
1.1 OLED display
Flex PCB is mainly used as part of signal connection for folding, rotating, and other hinge parts in smartphones. One of the typical applications is OLED display. OLED display, referring to Organic Light Emitting Diode, is a new generation of display screens. Compared with traditional display screens, flexible screens are thinner, lighter, bendable, and are of low power consumption and rich colors. They are widely used in new generation electronic products such as curved displays, foldable phones, and wearable devices. Flex PCB is more suitable for electronic products using flexible screens for its light, thin and bendable characteristics.
Take folding screen phone as an example. In response to the trend of smartphones towards lighter, thinner, and more portable, manufacturers of mobile phones have successively released folding screen phones. In October 2018, Royole Technology released the world's first foldable smartphone FlexPai, while in February 2019, Samsung released the Galaxy Fold, and Huawei released the folding full-screen phone Mate X. The OLED technology has been constantly improved and gains in use for folding-screen phones, bringing incremental demand for Flex PCB.
Figure 2: Samsung OLED display
1.2 Multi-functions of smartphones
To seize market share and stimulate consumers' purchase willingness, mobile phone brands continue to innovate and enrich product functions, resulting in a higher demand for PCBs especially, Flex PCB. At first, Flex PCB is used for LCD panels, LCD modules, camera modules, buttons, and batteries in mobile phones. The introduction of biometrics technology brings new applications of fingerprint, face recognition modules, followed by multiple cameras and other innovative functions. Thus, more electronics components are needed to support the increasing features in volumetrically limited spaces, which drives rigid PCB to be replaced by Flex PCB.
As smartphones continue to evolve with more advanced features, the use of Flex PCB increases accordingly. For example, in the iPhone series, Flex PCB has covered the applications of the flashlight & power cord, antenna, vibrator, speaker, side button, camera, 3D Sensing, motherboard, display and touch module, HOME button, SIM card holder, independent backlight, headphone jack, and microphone.
Figure 3: Flex PCB in iPhone
2. Medical wearable devices
Medical wearable devices are used to collect all varieties of physiological data for diagnosis and personal health use. Attaching directly to the people, they need to be comfortable and unobtrusive, which requires very dense layouts and a compact package of the products. Flex PCB enables many medical devices to become smaller, smarter, and lighter due to its flexibility and high circuit density characteristics. Thus, they are widely used in wristwatches, hearing-assist devices, wearable monitoring devices, etc.
The COVID-19 pandemic has highlighted the potential of wearable electronic devices in healthcare. They allow physiological signals to be continuously monitored, for which they can be used in the early detection of asymptomatic and pre-symptomatic cases of COVID-19. With such devices becoming smaller while increasing in complexity, the demand for Flex PCB continues to grow.
Figure 4: Covid sensor ring detects subtle symptoms
3. Automotive electronics
New energy vehicles are the mainstream for the future development of the automotive industry. As a traditional line carrier, automotive wiring harnesses are relatively heavy and complicated in connection, which cannot comply with the continuously increasing quantities of electronic components for new energy vehicles. However, Flex PCB offers freedom of designing while being able to withstand millions of dynamic bending without damaging the wire, making it an ideal replacement for wire harnesses. Besides, Flex PCB has high reliability, heat resistance, and durability characteristics suitable for automotive electronic components in harsh environments. It is now used for LED car lights, gearboxes, sensors, BMS, car display, navigation, entertainment system, and other car devices in the new energy vehicles.
Figure 5: Flex PCB in automotive light
With continued innovation and development of the sensor technology, the potential of automotive electronics has become increasingly apparent, which is expected to become an important growth impetus for the Flex PCB market.
Conclusion
Miniaturization is a key trend of future electronics and Flex PCB enables the electronics to become smaller, thinner, lighter for its flexing property. The growth of Flex PCB has primarily been driven by the increasing demand for consumer electronics, wearable devices, and automotive electronics, while the rapid development of such electronics is imposing a higher requirement on Flex PCB quality and technology.
Under this circumstance, many Flex PCB manufactures are investing in better machinery to improve their Flex PCB capabilities. As a leading Flex PCB manufacturer with over 10 years of experience, PCBgogo continues to update its technology and production equipment so as to serve the increasingly complex needs of its customers. PCBgogo is well prepared to offer you expert support and manufacture your Flex PCB for your next projects.