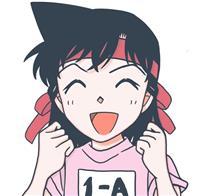
Flexible Printed Circuits – How to Choose the Right Material for Your Application
Flexible printed circuit (FPC) technologies have been proven as reliable and effective solutions to dynamic environments. Design circuits is supported by most modern E-CAD tools, but material selection for your FPC application can be a tricky process. In this article we will consider material selection for the FPC substrate, conductor, coverlay, surface finish, and stiffeners.
Substrate
The substrate is the core of a flex circuit stackup. Polyimide (PI) and Polyester (PET) are a fantastic choice for the vast majority of FPC applications as they offer a wide range of cost and performance to meet designers’ needs.
In general, PET is a low-cost solution with great tear strength and thickness for most applications but falls short in its temperature rating. Since soldering would melt the material, polyester flex circuits use a conductive epoxy paste which acts like a glue attaching devices to the conductors. The strength of the bond is generally 1/3 that of a soldered connection, but it is still highly reliable and low-cost method of assembly.
Polyimide (PI) is the most popular FPC substrate material due to its unbeatable cost to performance ratio. Unlike PET, its high temperature rating allows for multiple solder reflows. Polyimide’s great flexibility make it an ideal candidate for dynamic environments.
Other niche polymer materials, such as PTFE and PVDF, excel in critical industrial and communications applications, but are very expensive.
Conductor
Working our way out, the conductor choice is generally decided by the substrate. PET substrates are limited to using a silver ink as the conductor element, while Polyimide and other FPC materials use thin copper foils (electrodeposited (ED) or rolled annealed (RA) copper). Here are a few criteria to consider when selecting between ED and RA copper.
· Flexibility – The rolling process in creating RA copper makes it better suited for frequent
bending.
· Extensibility – RA copper can be extended about 20-45%, great for flexible applications.
· Conductivity – The electrolysis method of creating ED copper results in much better
conductivity, ideal for high-current, low weight applications.
· Insertion Loss – RA copper’s smooth surface makes it an ideal material for high-frequency
applications due to low insertion loss.
· Manufacturing Cost – ED copper requires less manufacturing steps, and is therefore is cheaper than RA copper.
Coverlay
Coverlay’s primary function is to provide protection to the external copper foil from corrosion and abrasion. For FPC’s, consider between a solid sheet polyimide coverlay and flexible solder mask.
Polyimide coverlay is generally the preferred material for FPC applications as it shares the same flexibility with the substrate. It also has a great dielectric voltage withstanding of about 3KV/1mil of thickness, making it a great insulator.
Flexible solder mask is essentially the same material as used in rigid printed circuit boards, except it has a flex agent added for FPC applications. It is more rigid that coverlay and is only rated for around 500V/1 mil of thickness. The other limiting factor of flexible solder mask is that it is not suitable for stiffener application or shielded layers in the same regions due to a weakened bond. However, it is preferred in high-density component regions as it allows for smaller solder mask slivers.
Consider using coverlay in frequent bend areas and flexible solder mask in zones densely populated with fine-pitch components.
Surface Finish
Selecting a surface finish material for an FPC will mostly impact the shelf life of a design as well as the quality of the solder bond between component and pad. Use the guide below as a reference for selecting a surface finish material.
Note: HASL, a common surface finish for rigid printed circuit boards, is generally not used for FPC applications due to the high temperatures used in the application process which might damage the circuit.
Stiffeners
Interfacing with zero-insertion-force (ZIF) connectors, reinforcing zones with soldered components, protecting solder joints from cracking, and accounting for heat dissipation are all important considerations when selecting your material for a stiffener.
FR-4 and Polyimide are great cost-effective stiffener choices for dynamic applications. They provide stress relief for large connectors or additional thickness for meeting the minimum requires of a ZIF connector. FR-4 and Polyimide can also provide support for component regions or localized bend zones.
Aluminum and Stainless Steel provide even greater stiffness without adding unnecessary thickness but cost more. Aluminum is also sometimes also sometimes used for its heat dissipation properties.
Conclusion
Material choice is a critical factor when designing a flexible PCB. Ask yourself what environments your design needs to work in, your assembly timeline, and what manufacturing processes might impact the materials selected. It may be difficult to strike a balance between cost and performance, but don’t hesitate to reach out to your manufacturer for consultation. The experts at PCBgogo can help guide you to choosing the right material for your custom application.