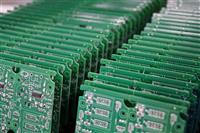
Introduction
In the ever-evolving landscape of electronics manufacturing, Surface Mount Technology (SMT) has become a cornerstone of printed circuit board (PCB) production. SMT has revolutionized PCB assembly, replacing traditional through-hole technology in many areas and unlocking new potentials in terms of design flexibility, production efficiency, and compact electronic devices. For companies like PCBGOGO that specialize in PCB prototyping, assembly, and manufacturing, understanding and mastering SMT is crucial for delivering high-performance products.
This article dives deep into SMT's applications, advantages, and its synergy with through-hole technology, covering essential processes used in PCB assembly. Whether you are a designer, engineer, or manufacturer, mastering SMT will streamline your production and help you leverage the full potential of modern PCB solutions.
What is Surface Mount Technology (SMT)?
Surface Mount Technology (SMT) is a method for assembling PCBs by directly mounting components on the surface of the board, as opposed to inserting them through holes (as done with through-hole technology). SMT components are smaller, lighter, and more efficient, making them ideal for compact and high-density electronic designs. This technique enables automated assembly, resulting in faster production times, lower costs, and fewer defects.
With SMT, you can fit more components on smaller boards, which translates to higher performance and more features without increasing the physical size of the product. PCBs that leverage SMT are easier to mass-produce thanks to automation, which makes the technology a perfect fit for industries that need rapid product cycles.
SMT vs. Through-Hole Technology: A Comparative Overview
Although SMT is now the dominant PCB assembly method, through-hole technology (THT) still holds relevance for certain applications, particularly where high mechanical strength or durability is required. Let’s compare the two approaches:
Features | SMT | Through-Hole Technology (THT) |
Component size | Smaller and compact | Larger components |
Assembly process | Automated with pick-and-place machines | Manual or semi-automated |
Mechanical strength | Lower mechanical strength | Higher mechanical strength |
Application | Consumer electronics, smartphones | Power devices, connectors, transformers |
Cost | Lower overall cost | Higher cost due to labor-intensive process |
PCB density | Higher density possible | Limited due to larger components |
Many manufacturers, including PCBGOGO, utilize a hybrid approach—combining SMT with through-hole components—ensuring that the final product benefits from the strengths of both technologies.
The Advantages of SMT in PCB Assembly
Surface Mount Technology (SMT) has become the go-to method for assembling printed circuit boards (PCBs), thanks to its efficiency, scalability, and compatibility with modern electronic designs. For industries ranging from consumer electronics to automotive systems, SMT offers the perfect balance between efficiency and reliability, making it indispensable in today’s competitive market. Below are the key advantages of SMT in PCB assembly that make it a preferred choice for manufacturers worldwide:
1. Smaller and Lighter Components
SMT components are compact and lightweight compared to those used in through-hole technology (THT). This makes it easier to design products with higher functionality while keeping their physical size small. Devices like smartphones, wearables, and medical equipment greatly benefit from this miniaturization, allowing manufacturers to offer more features in smaller packages.
2. High Component Density for Complex Designs
One of the standout features of SMT is that it allows components to be placed on both sides of the PCB, increasing the board’s functionality without increasing its size. This capability supports the creation of high-performance circuits required for compact devices like laptops, sensors, and smart appliances. SMT enables higher integration levels, which is essential for meeting the demands of today’s electronic products.
3. Faster Assembly with Automation
SMT processes are largely automated, using pick-and-place machines that can mount thousands of components in minutes with incredible accuracy. This speeds up production and ensures consistency across large batches. Automated assembly reduces human error and minimizes defects, making SMT a great option for manufacturers who need quick turnaround times and high-volume production.
4. Reduced Manufacturing Costs
Although initial investments in SMT equipment may be high, the long-term savings are significant. SMT assembly requires less manual labor than through-hole methods, and the smaller components cost less to produce. Additionally, because more components can fit on a single PCB, the overall number of boards required for a project is often reduced, further cutting manufacturing costs.
5. Better Electrical Performance
The shorter leads of SMT components reduce the risk of signal interference and parasitic capacitance, leading to improved electrical performance. This makes SMT an excellent choice for circuits requiring high-frequency performance, such as radio frequency (RF) modules, communication devices, and high-speed data processors.
6. Enhanced Design Flexibility
With the ability to fit more components onto a single board, SMT offers greater flexibility in circuit design. Engineers can experiment with different configurations without worrying about space limitations, enabling them to develop innovative solutions. The use of multi-layer PCBs is also easier with SMT, allowing more complex circuits to fit into compact products.
7. Supports Lightweight, Portable Products
In today’s consumer market, products need to be lightweight and portable. SMT makes this possible by eliminating the need for heavy through-hole components, contributing to the development of sleek, lightweight designs. From smartphones to fitness trackers, SMT plays a critical role in modernizing electronics for portability and convenience.
8. Reliability and Durability
The automated precision of SMT assembly ensures fewer defects, contributing to better reliability in end products. The strong solder joints formed during reflow soldering provide stable connections, even in compact or densely populated boards. As a result, SMT-assembled PCBs can withstand thermal cycles and vibrations, making them suitable for both consumer electronics and industrial applications.
9. Environmentally Friendly Production
SMT assembly typically requires less material than through-hole assembly. The smaller size of components means fewer raw materials are used, contributing to environmentally conscious production. Additionally, automated SMT processes reduce the amount of waste generated compared to more labor-intensive methods.
10. Scalable for Mass Production
SMT’s reliance on automated machinery makes it highly scalable. Whether you need a small batch for prototyping or mass production, the process can be adapted to meet demand without compromising on quality. This scalability is essential for industries with high product turnover, such as consumer electronics, where speed and efficiency are critical.
The Role of PCBGOGO in SMT PCB Manufacturing
PCBGOGO is a leading PCB manufacturer offering high-quality PCB prototypes, manufacturing, and assembly services. Their expertise in SMT assembly ensures that customers receive reliable and efficient solutions tailored to their needs. From small-scale prototyping to large-volume production, PCBGOGO’s advanced equipment and experienced engineers streamline the entire PCB assembly process.
Services Offered by PCBGOGO for SMT Assembly
Prototyping and Testing
PCBGOGO provides fast and cost-effective prototyping services. This ensures that designs are validated before moving to full-scale production, helping customers detect potential issues early in the process.
Turnkey PCB Assembly
With both SMT and through-hole assembly capabilities, PCBGOGO offers complete turnkey solutions. They handle everything from component sourcing to PCB fabrication and assembly, ensuring seamless production.
Quality Control and Inspection
PCBGOGO follows stringent quality control measures, including Automated Optical Inspection (AOI) and X-ray testing, to ensure that every PCB meets international standards. Their commitment to quality ensures defect-free products for customers across industries.
Key Processes in SMT Assembly
1. Solder Paste Printing
The first step in SMT assembly involves applying solder paste to the areas of the PCB where components will be placed. This paste consists of a mixture of tiny metal solder particles and flux, which helps facilitate the soldering process.
· Stencil Printing: A stencil is used to ensure the solder paste is applied only on the designated solder pads. The PCB passes under the stencil, and the paste is spread evenly over it with a squeegee.
· Precision: Proper alignment of the stencil and board is critical to avoid issues like solder bridging or misaligned components.
2. Component Placement with Pick-and-Place Machines
Once the solder paste is applied, pick-and-place machines take over the task of placing components on the board. These automated machines use suction tools or mechanical arms to accurately position Surface Mount Devices (SMDs) on the PCB.
· Speed and Accuracy: Modern machines can place thousands of components per hour with incredible precision.
· Multiple Components: Both small passive components (like resistors and capacitors) and integrated circuits (ICs) can be mounted efficiently.
This step is essential in ensuring component alignment, as even a slight misplacement can affect the PCB’s performance.
3. Reflow Soldering
Once the components are in place, the board passes through a reflow oven. Heat causes the solder paste to melt and bond the components to the board. After cooling, the solder solidifies, creating reliable connections.
· Heating Profile: The board goes through several temperature zones—preheating, soaking, reflow, and cooling. This gradual temperature increase ensures the solder melts properly without damaging sensitive components.
· Solid Bonding: Once the board exits the oven and cools, the solder solidifies, securing the components in place.
Reflow soldering is a critical step to ensure the durability and performance of the assembled PCB.
4. Inspection and Testing
To ensure quality, SMT assemblies undergo Automated Optical Inspection (AOI). Some PCBs may also require X-ray inspection to verify hidden solder joints. Functional testing is performed to validate the circuit’s performance.
? Automated Optical Inspection (AOI)
After reflow soldering, the board undergoes Automated Optical Inspection (AOI) to detect any defects, such as missing components, solder bridges, or misalignments. AOI systems use high-resolution cameras to scan the board and compare it with design specifications.
· Defect Detection: AOI helps catch issues early, reducing the need for rework.
· Non-Destructive Testing: This process ensures quality without damaging the PCB or components.
? X-Ray Inspection (for Hidden Joints)
For boards with Ball Grid Array (BGA) or other components with hidden solder joints, X-ray inspection is used to verify connections. This technique helps identify problems like cold joints or solder voids, which can affect the board’s performance over time.
? Functional Testing (FCT)
To ensure the assembled PCB performs as expected, it undergoes functional testing. In this step, test probes are connected to the board’s key points to verify voltage, current, and signal flow.
· Simulation of Operating Conditions: The PCB is tested under conditions similar to its intended application.
· Fault Detection: Any issues in signal transmission or power distribution are identified and corrected at this stage.
? Rework and Repair (if needed)
If defects are identified during inspection or testing, rework is performed to correct the issues. For minor defects like solder bridges or misalignments, operators manually adjust the components or re-solder the affected areas.
· Precision Repairs: Specialized tools like hot air rework stations help make targeted repairs without damaging nearby components.
· Minimizing Waste: Reworking boards ensures minimal waste and reduces the need for remanufacturing.
5. Cleaning and Final Inspection
After rework, the PCB undergoes cleaning to remove any flux residue, ensuring that no contaminants are left that could affect performance. The board then passes through final inspections to confirm it meets design requirements.
· Visual Inspection: Operators perform a final visual check to catch any remaining defects.
· Compliance Testing: The board is tested to ensure it meets industry standards and customer specifications.
6. Final Assembly and Packaging
Once the assembled and inspected PCBs pass all tests, they are carefully packaged to prevent damage during shipping. Proper packaging ensures that moisture and static charges do not affect the boards.
· Moisture-Resistant Packaging: PCBs are often sealed in anti-static bags with moisture indicators to prevent damage.
· Labeling and Traceability: Serial numbers and barcodes are added to track the boards during shipping and ensure traceability.
SMT and Through-Hole: Finding the Perfect Balance
While SMT is ideal for high-volume production and compact designs, through-hole technology remains relevant for specific applications. For example, connectors, transformers, and components requiring mechanical stability still rely on through-hole assembly.
Many manufacturers, including PCBGOGO, adopt a hybrid assembly approach that combines SMT and through-hole components. This strategy allows engineers to optimize performance while ensuring that products meet the necessary mechanical and durability standards.
A hybrid PCB assembly combines SMT and through-hole technologies to achieve the best of both worlds. This approach allows manufacturers to leverage the strengths of SMT—like compact size and automated production—while maintaining the mechanical strength provided by through-hole components.
Many products, especially those in the automotive, aerospace, and industrial sectors, require this hybrid strategy.
Hybrid PCB Assembly:
Hybrid PCB assembly combines Surface Mount Technology (SMT) and Through-Hole Technology (THT) on a single printed circuit board (PCB) to leverage the strengths of both methods. This approach provides flexibility, enabling manufacturers to build high-performance, compact, and reliable electronic products that meet the complex needs of modern industries, such as telecommunications, automotive, medical devices, and aerospace.
What Is Hybrid PCB Assembly?
Hybrid PCB assembly integrates SMT and THT components on the same PCB. SMT components are placed directly on the board’s surface, while THT components are inserted through drilled holes and soldered to the board. This combination offers greater design versatility and mechanical durability, especially in products that require both miniaturization and stability.
Key Components of Hybrid PCB Assembly
· Surface Mount Components (SMDs):
Used for small, high-frequency, and space-saving components such as resistors, capacitors, ICs, and LEDs.
· Through-Hole Components:
Ideal for connectors, switches, relays, and large capacitors that require a strong mechanical bond.
· Mixed Signal Boards:
Boards containing both analog and digital circuits benefit from hybrid assembly, as SMT components handle the digital signals, while THT components ensure reliable analog connections.
Benefits of Hybrid PCB Assembly
1. Design Versatility
Hybrid assembly allows engineers to integrate high-density SMT components and mechanically strong THT components on the same board. This versatility supports complex designs, such as mixed-signal circuits and multi-layer PCBs.
2. Improved Mechanical Stability
THT components, with their leads passing through the board, offer higher mechanical strength, making hybrid PCBs ideal for products subject to vibration or stress, such as automotive control units or industrial machinery.
3. Optimized Performance
The combination of SMT and THT ensures optimal electrical and mechanical performance, meeting the needs of applications that require both high-frequency operations and rugged durability.
4. Cost-Effective Production
By leveraging automated SMT processes alongside selective THT insertion, hybrid assembly can achieve faster production and lower costs compared to fully THT designs.
SMT Challenges and Solutions
Despite its many advantages, SMT presents some challenges in PCB assembly. Here’s a look at common obstacles and how PCBGOGO addresses them:
Component Handling Issues
SMT components are delicate and prone to damage during handling. PCBGOGO uses state-of-the-art equipment and trained technicians to minimize handling risks and ensure component integrity.
Solder Joint Defects
Issues such as solder bridging and cold joints can occur during reflow soldering. PCBGOGO mitigates these problems through precise stencil design, optimized reflow profiles, and thorough inspections.
Moisture Sensitivity
Some SMT components are moisture-sensitive and can degrade if not handled correctly. PCBGOGO follows strict storage and handling protocols to prevent moisture-related issues, including the use of desiccants and moisture-controlled environments.
The Future of SMT in PCB Manufacturing
As the electronics industry continues to evolve, SMT will play an even more critical role in shaping the future of PCB manufacturing. Trends such as miniaturization, flexible PCBs, and advanced IoT applications are driving the need for more innovative SMT solutions. Manufacturers like PCBGOGO are at the forefront of these developments, offering cutting-edge services that meet the demands of modern electronics.
Advancements in SMT equipment—such as 3D printing and AI-driven inspection systems—will further enhance the efficiency and accuracy of PCB assembly. These innovations will open new doors for faster production, lower costs, and enhanced product performance.
Conclusion
Surface Mount Technology (SMT) is unlocking unprecedented potential in PCB assembly, enabling manufacturers to create compact, high-performance, and cost-effective electronic products. By understanding the nuances of SMT and integrating it with through-hole technology where necessary, companies can strike the perfect balance between performance and durability.
PCBGOGO’s expertise in SMT assembly ensures that customers receive world-class solutions tailored to their unique needs. Whether developing prototypes or scaling up for mass production, mastering SMT is essential to staying ahead in the competitive electronics market. With PCBGOGO’s support, you can streamline your production processes and unlock the full potential of your PCB designs.