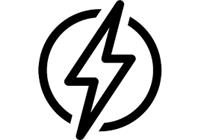
Some electronics hobbyists may have known how to make a custom PCB in-house. However, do you know how do printed circuit boards manufacture in streamlines or factories?
PCB manufacturing is more related to chemical and photo-logy than physics. Most PCB manufacturers adopt the dry film developing technique to print circuits into the boards. They also use chemical reactions to electroplate vias and holes on the PCBs.
What is Printed Circuit Boards?
A printed circuit board (PCB) is the board base for physically supporting and wiring the surface-mounted and socketed components in most electronics. In applications where fine conductive traces are needed, such as computers, PCBs are made by a photolithographic process, in a larger-scale version of the way conductive paths in processors are made.
Electronic components are typically placed by the machine onto a finished PCB that has solder joints in place. The PCB bakes in a reflow oven to melt the solder, which joins the connections. Most PCBs are made from fiberglass or glass-reinforced plastics with copper traces.
PCBs can be single-layer for simple electronic devices and can be multi-layer for complex hardware, such as computer graphics cards and motherboards, and may have up to twelve layers. PCBs are most often green but they can come in any color. Other methods of PCB manufacturing include silk screening and CNC milling.
Image: PCBGOGO Red FR-4 Printed Circuit Board
Light Control In PCB Factory
Due to the precision and harshness of printed circuit boards, each PCB workshop environment requires high standard management. Some workshops are even exposed to the "yellow light" day after day because the light-sensitive dry film is not sensitive to yellow light, which will not be exposed. This is the same reason why photographic negatives cannot be exposed to sunlight but are fine in the darkroom under green light. A class 10,000 cleanroom dedicated to exposure. The reason the exposure machine completes the image transfer work in a cleanroom is that dust refracts light, which inevitably distorts the line drawing transferred to the dry film. The more serious thing is that the dust particles will stick to the board surface blocking light and causing impurities to break or short circuit.
Image: Exposure Room of PCBGOGO Factory
Moisture Control in PCB Factory
And humidity is also one of the indicators that need to be strictly controlled. It is a very critical and strictly controlled indicator of the manufacturing process. Low humidity may lead to dryness, increased electrostatic discharge, and dust. It could be easier to clog stencil holes and lead to wearing the stencil, so low humidity has been proven to directly affect and reduce productivity. Meanwhile, high humidity will cause the material to absorb too much moisture from the air, leading to delamination, popcorn effect, and weld balls. Moisture also reduces the TG value of the material and increases dynamic warpage during reflow soldering.
Almost all solid surfaces (e.g. metals, glass, ceramics, silicon, etc.) have a layer (mono- or multi-molecular layer) for moisture-absorbing that is visible when the surface temperature equals the dew point temperature of the surrounding air (depending on temperature, humidity, and air pressure). Metal-to-metal friction increases with decreasing humidity, and at 20% RH and below, friction increases 1.5 times more than at 80% RH conditions.
Porous or moisture-absorbing surfaces (epoxies, plastics, solder, etc.) tend to absorb these absorbent layers, and even when the surface temperature is below the dew point (condensation), the moisture-containing absorbent layer is not visible on the material surface.
It is the water in the monomolecular absorbent layers on these surfaces that penetrates the molded device (MSD), and the moisture absorbed by these monomolecular absorbent layers eventually leads to the popcorn effect during reflow when the monomolecular absorbent layers approach 20 layers of in thickness.
Humidity has many effects on production and manufacturing. Generally, moisture is invisible (except for weight gain), but the consequences are porosity, voids, solder spatter, solder balls, and bottom fill voids.
The control of moisture and humidity is very important in any process processing, and the lighter the abnormal appearance of the body surface, the heavier the manufactured product is not qualified. Therefore, the usual workshop is to ensure that the surface of the substrate moisture and humidity control properly, to ensure that the production of finished products in the production process of environmental indicators are within the specified.
Image: PCB Assembly From PCBGOGO Factory
Conclusion
In PCB manufacturing, the control of light and moisture is restricted. Every mistake in the workshop environment or workers’ operation leads to bad quality of PCBs. Engineers need to understand the scale and experience of PCB manufacturers as a partner. The most intuitive way to do this is to find the certifications of that PCB manufacturer. Generally, the ISO 9001 certificate reveals high-quality PCB factory management, and it is a criterion for PCB manufacturers.
If you are looking for a PCB manufacturer, you can consider PCBGOGO as a partner. With over ten years of manufacturing experience, PCBGOGO has qualified with international quality control organizations.