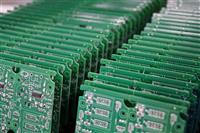
In today’s fast-paced world of electronics, turning ideas into reality requires precision, speed, and expertise. As innovations in technology continue to accelerate, industries are increasingly relying on partners who can streamline the manufacturing process from start to finish. That’s where PCBGOGO steps in, delivering seamless turnkey PCB assembly services that transform blueprints into fully functional printed circuit boards (PCBs). This article delves into PCBGOGO’s expertise, innovations, and the customer journey that ensures every design is executed with excellence.
The process of PCB assembly is intricate and requires meticulous attention to detail. From blueprint to fully assembled board, each step contributes to creating a reliable product. Manufacturers like PCBGOGO simplify this complex journey by offering turnkey solutions, including PCB assembly and quality control. Their expertise ensures that every PCB, whether for a prototype or large-scale production, meets the highest industry standards.
PCBGOGO: A Trusted Name in PCB Manufacturing and Assembly
PCBGOGO is a renowned player in the world of PCB assembly and manufacturing, with a reputation built on reliability, quality, and competitive pricing. Established with a vision to serve designers, startups, and large-scale manufacturers alike, PCBGOGO has become synonymous with high-performance PCB solutions. The company specializes in turnkey PCB assembly, making it a one-stop destination for those looking to simplify their production cycles.
PCBGOGO offers end-to-end services, from PCB prototyping and fabrication to component sourcing and final assembly. Whether you are building a prototype or mass-producing a product, the company ensures that every step of the process aligns with international quality standards. Their clients span industries including telecommunications, consumer electronics, automotive, and medical devices, reinforcing PCBGOGO’s commitment to versatile and robust manufacturing.
The Power of Turnkey PCB Assembly: Simplifying the Process
One of the biggest challenges in PCB manufacturing is managing multiple stages, from sourcing components to ensuring accurate assembly. Traditional assembly methods can involve multiple suppliers, increased lead times, and communication hurdles, leading to delays and quality issues. Turnkey PCB assembly eliminates these challenges by consolidating every step into a streamlined, managed process handled by a single provider.
At PCBGOGO, turnkey assembly:
Component Procurement: The company leverages its extensive supplier network to source high-quality parts, saving clients from the headache of locating reliable vendors.
PCB Fabrication and Prototyping: PCBGOGO offers prototyping services, helping engineers detect design flaws early in the process, thereby reducing errors during mass production.
Assembly and Testing: The company assembles the PCBs with precision and runs rigorous tests to ensure every board meets performance and reliability standards.
Quality Control and Compliance: All PCBs are manufactured according to industry certifications, including ISO9001, UL, and RoHS compliance, ensuring superior quality.
PCB Assembly: from blueprint to high quality assembled PCB
The journey of a printed circuit board (PCB) begins with a vision and a blueprint and ends with a fully assembled, high-quality product. This step-by-step process ensures that every board meets the specifications for performance, durability, and functionality. Below, we explore the key stages involved in manufacturing and assembling a PCB, from initial design to final inspection.
1. Design and Blueprint Creation
The foundation of any PCB project starts with the circuit design and layout. Engineers create detailed schematics and translate them into Gerber files, which provide the essential data needed for manufacturing. These files contain information on the board’s copper layers, holes, vias, solder masks, and silkscreens.
Key Steps:
? Schematic Design: This electrical diagram outlines the circuit’s function and connections.
? Layout Design: Software tools such as Altium, Eagle, or KiCAD convert the schematic into a physical PCB layout, determining the placement of components and copper traces.
? Design Rule Check (DRC): Automated checks ensure that the design follows manufacturing constraints, minimizing errors.
2. Material Selection and Layering
Once the design is finalized, the manufacturer selects the base material, often FR4, a glass-reinforced epoxy laminate. If the PCB needs additional layers for complex applications, multilayer boards are created by stacking and bonding multiple copper and insulating layers.
Types of PCB Layers:
· Single-layer: For simple circuits, typically used in basic consumer electronics.
· Multilayer PCBs: Essential for complex devices like smartphones, featuring 4 to 12 layers.
· High-frequency materials: Used for specialized applications, such as RF circuits.
3. Patterning and Etching
The copper-clad laminate undergoes a photolithography process to transfer the circuit design onto the board. A layer of photosensitive material, or resist, is applied to the surface. The Gerber file design is printed on a transparent film and aligned with the board.
Steps in Etching:
· Exposure: The PCB is exposed to UV light, which hardens the desired pattern areas.
· Development: The unexposed areas are washed away, leaving behind the circuit pattern.
· Etching: The board is immersed in an etching solution (e.g., ferric chloride or ammonium persulfate) to remove unwanted copper, leaving behind the traces.
4. Drilling and Plating
The next step involves drilling holes and vias into the board to connect different layers. Manufacturers use precision CNC drilling machines to ensure accuracy. After drilling, the board undergoes a plating process to coat the inner walls of the holes with copper, allowing electrical connections between layers.
Types of Vias:
· Through-hole vias: Connect all layers of the board.
· Blind vias: Connect outer layers to inner layers without passing through the entire board.
· Buried vias: Located within internal layers and do not extend to the surface.
5. Solder Mask and Silkscreen Application
A solder mask is applied to the board to insulate and protect the copper traces, leaving only the areas needed for soldering exposed. The solder mask, typically green, prevents short circuits and oxidation.
After the mask is applied, silkscreen printing adds labels, logos, and component indicators on the PCB to guide assembly.
6. Surface Finishing
The exposed copper pads on the board need surface finishing to ensure smooth soldering during assembly. Manufacturers apply different surface finishes depending on the application, including:
· HASL (Hot Air Solder Leveling): Common and cost-effective, suitable for general-purpose PCBs.
· ENIG (Electroless Nickel Immersion Gold): Ideal for boards requiring higher corrosion resistance.
· OSP (Organic Solderability Preservative): Environmentally friendly and used for simpler applications.
7. PCB Assembly (PCBA)
With the bare board ready, it moves on to the assembly stage, where components are placed and soldered onto the PCB.
There are two primary methods for assembling components:
Surface-Mount Technology (SMT):
Components are mounted directly onto the board's surface using solder paste. A pick-and-place machine arranges the parts with precision, followed by reflow soldering to secure them. SMT is ideal for compact designs and high-speed assembly.
Key Features of Surface-Mount Technology (SMT)
1. Compact Size: SMT components (SMDs) are smaller, enabling miniaturized and lightweight designs.
2. High Component Density: Supports placing more components on smaller PCBs, including both sides of the board.
3. Automated Assembly: Uses pick-and-place machines for fast, precise, and efficient manufacturing.
4. Reduced Drilling Requirements: No need for through-hole drilling, speeding up production.
5. Improved Performance: Lower inductance and resistance, enhancing signal quality and reliability.
6. Cost-Effective: Reduces material and labor costs through automation and smaller components.
7. Versatility: Ideal for mass production and complex applications, from consumer electronics to medical devices.
Through-Hole Assembly:
Components with leads are inserted into drilled holes and soldered manually or by wave soldering. This method is often used for connectors and components that require mechanical strength.
Key Features of Through-Hole Technology (THT)
1. Strong Mechanical Bond: Components are soldered through drilled holes, offering better durability and reliability under mechanical stress.
2. Ideal for Prototyping: Easier to manually solder and replace components, making it suitable for testing and development.
3. High Power Handling: Suitable for components like transformers and capacitors that require higher current or voltage.
4. Enhanced Temperature Resistance: Performs better in harsh environments, such as industrial and automotive applications.
5. Secure Connections: Reduces the risk of component detachment due to vibrations or shocks.
6. Simpler Inspection: Solder joints are visible, making quality control and troubleshooting easier.
7. Limited Component Density: Less compact than SMT, making it more suitable for larger components or low-density designs.
8. Testing and Quality Control
To ensure that every assembled PCB meets functional and performance standards, manufacturers conduct various tests:
· Automated Optical Inspection (AOI): High-resolution cameras scan the board to detect soldering defects, misplaced components, or missing parts.
· X-ray Inspection: Used for boards with hidden connections, such as BGAs (Ball Grid Arrays).
· In-Circuit Testing (ICT): Verifies that the components are correctly installed and electrically functional.
· Functional Testing: Simulates real-world conditions to check if the board performs as intended.
9. Packaging and Delivery
Once the boards pass all quality checks, they are cleaned and packaged carefully to prevent damage during shipping. Anti-static bags or bubble wrap are used to protect against electrostatic discharge (ESD). Manufacturers also include labels with part numbers and batch information for easy tracking.
10. Final Quality Assurance and Customer Feedback
After delivery, the manufacturer stays in contact with the client to gather feedback and provide any necessary support. Some manufacturers offer post-delivery services, such as rework or maintenance on boards that need adjustments.
Advancements in Turnkey PCB Assembly at PCBGOGO
PCBGOGO has continuously evolved to incorporate the latest technologies and meet the increasing demands of modern electronics. Here’s what sets their turnkey PCB assembly apart:
1. State-of-the-Art Equipment
PCBGOGO's assembly line features cutting-edge equipment, including automatic pick-and-place machines, reflow ovens, and soldering stations. This technology ensures high accuracy, even with intricate and complex PCB designs, while keeping errors to a minimum.
2. Quick Turnaround Times
In a world driven by deadlines, PCBGOGO offers fast turnaround times. Their in-house capabilities allow them to deliver prototypes within 24 hours and production-ready assemblies within days, helping customers launch products faster and stay ahead of the competition.
3. Flexible Production Runs
Whether it’s a single prototype or large-scale production, PCBGOGO handles both with ease. They provide small-batch production options, which are essential for startups and design engineers, alongside mass production capabilities for high-volume orders.
4. Strict Quality Assurance Protocols
PCBGOGO conducts thorough inspections at every stage, including automated optical inspection (AOI) and X-ray testing for complex boards. Their strict quality control processes guarantee that each PCB delivered matches the highest performance standards.
PCB Assembly: From Concept to Reality
The journey from idea to fully assembled PCB is made seamless through PCBGOGO’s turnkey services. Here’s a step-by-step overview of how their process ensures success:
1. Blueprint and Design Submission
Clients submit their designs, including schematics, Gerber files, and BOM (bill of materials) lists, directly through PCBGOGO’s online platform. Their team also offers DFM (Design for Manufacturability) services, identifying any potential design flaws early on.
2. Component Sourcing and Procurement
PCBGOGO’s strong partnerships with reliable global suppliers mean components are sourced quickly and cost-effectively. They also offer alternative parts when specific components are unavailable or outdated, reducing lead times without compromising quality.
3. Fabrication and Prototyping
Once the design is finalized, PCBGOGO begins the fabrication process. They offer both single-layer and multilayer PCBs with a range of material choices, ensuring the design specifications match the intended application. For complex designs, their rapid prototyping services help test functionality before moving to mass production.
4. Assembly and Soldering Techniques
PCBGOGO’s assembly services include both surface-mount technology (SMT) and through-hole assembly, depending on the project’s needs. Their experts ensure precise soldering techniques, which are crucial for the performance and longevity of the PCB.
5. Testing and Inspection
Every board undergoes a rigorous series of tests to identify potential defects. In addition to AOI, the company conducts in-circuit testing (ICT) and functional testing, simulating real-world scenarios to ensure each PCB performs as intended.
6. Shipping and Delivery
Once the assembly process is complete, the PCBs are packed securely and shipped promptly. PCBGOGO offers worldwide shipping, ensuring that clients receive their products wherever they are, without unnecessary delays.
Why Choose PCBGOGO?
PCBGOGO is not just another PCB manufacturer; they are a partner in innovation, helping customers turn visions into reality. Here are a few reasons why engineers and businesses trust them:
? All-in-One Solution: With turnkey PCB assembly, there’s no need to manage multiple suppliers.
? 24/7 Customer Support: PCBGOGO’s support team is available round-the-clock to answer questions and provide updates.
? Transparent Pricing: The company offers clear pricing with no hidden fees, helping clients stay within budget.
? Global Reach: With a wide client base and international shipping, PCBGOGO serves industries across the globe.
Real-World Applications of PCBGOGO’s PCBs
PCBGOGO’s PCBs are used in a wide variety of sectors, demonstrating their versatility and reliability:
? Consumer Electronics: From smartphones to wearables, PCBGOGO’s PCBs power many devices we use daily.
? Automotive Industry: Their PCBs are integrated into vehicles' control systems and infotainment units, ensuring both safety and performance.
? Medical Devices: Precision is paramount in healthcare, and PCBGOGO delivers reliable PCBs for diagnostic and monitoring equipment.
? IoT and Smart Devices: As IoT continues to grow, PCBGOGO plays a vital role in developing PCBs for smart homes and industrial automation.
Conclusion: Your Vision, PCBGOGO’s Expertise
Turning a design concept into a finished PCB requires more than just technical knowledge—it demands a partner with a deep understanding of every step in the process. PCBGOGO offers that expertise through its turnkey PCB assembly services, streamlining the journey from blueprint to final product. Their unwavering commitment to quality, innovation, and customer satisfaction makes them the ideal choice for engineers and businesses alike.
Whether you are a startup bringing a new product to life or a large corporation scaling production, PCBGOGO ensures your vision becomes reality with precision and efficiency. With their advanced manufacturing processes, quick turnarounds, and exceptional support, PCBGOGO is truly where craftsmanship meets innovation.
Ready to take your ideas from concept to reality? Contact PCBGOGO today to experience the seamless journey from blueprint to PCB assembly—because your vision deserves nothing but the best!