
The last time I tried to fabricate panels for a project in my home workshop, it was a difficult job. The cutouts were various shapes and I wanted them to look nice. So I carefully made some wood templates, attached them to the aluminum panels, and used a router to cut the holes. It took far too much effort and, although the results look ok, there are some obvious misalignments and minor flaws.
So, for my most recent project, I decided to get a panel made by a PCB shop. I thought I would have it made out of FR4, but found that the price for an aluminum panel was the same as FR4. So I ordered panels made from aluminum.
I ordered the PCB with good quality. The white solder mask is good and without flaws or gaps. The black silk screen lettering is flawless. I noticed that the larger holes are very slightly out of round. I suspect they were cut with a router rather than a drill. However, I had specified the holes to be slightly oversized, so it's not an issue for me. The edge of the rectangular cutout has a very small tab where it seems the router completed the cutout. This is hardly noticeable (perhaps 0.1 or 0.2 mm) and could be easily corrected with a hand file. Perhaps the biggest issue is that there are some scuffs and scratches in the surface of the solder mask that likely occurred as the panels were moved around during manufacturing and handling.
- Comments(1)
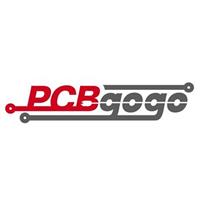
A****min
Sep 18.2019, 17:37:40
you potentially could use an alluminum panel as a capacitive touch button surface. An some clever use of copper might make for a really interesting contrasted panel. AS you say, an issue might be with how clean they arrive.