
A little while ago I had inquired here about the BRTRO-420 reflow oven, and found only one other user. I decided to buy one and have soldered some 30 or 40 boards with it by now, so I guess it is time to share my experience:
Build quality and electrical safety:
I opened the oven and had a look inside before using it for the first time. Overall, the build quality is pretty good. but the grounding of the enclosure is questionable. The ground wire from the inlet IEC receptacle is bolted down under one of the transformer mounting screws (typically an extra grounding bolt is required by regulations). In addition, the lower half of the enclosure is only grounded via the sheet metal screws that hold the upper half of the enclosure. Due to plenty of paint on all parts, this is a questionable contact. In my case there was continuity between top and bottom half, so I decided to leave it like that (and the room it is in is supplied via an 30mA RCD).
Proper Kapton tape has been used to secure the thermal insulation, so there is no nasty smell once the unit warms up (although there is a little ?hot equipment“ smell).
Usability, reflow etc.:
The unit can store 8 different reflow profiles. One can set the parameters (duration and final temperature) for pre-heat, heat, reflow, hold, and cool down steps. The four button operation is ok, although modifying a profile takes a lot of button presses of course. The logic of the final temperature for the cooldown step is weird, though: It is also used as starting temperature for the preheat step.
The unit has IR heaters with a power of 2500W (according to seller, I didn’t measure the power, but had a look at the electricity meter while the heaters were 100% on, and the numbers seem about right), plus one air intake, one air exhaust, and one circulation fan. There are 2 thermocouples hanging in the air above the circuit boards.
The temperature indication is somewhat noisy, but good enough. I don’t know how the single displayed value is calculated from the two TCs.
The heater power is just enough to follow roughly a usual heating profile (6 min for a complete solder process). I would recommend to do one empty run if the unit is cold, after that the initial PreHeat and Heat phases are followed more closely (without that, the heaters are basically 100% on until the reflow temp is reached).
PID control is ok, but could be better, especially I don’t like that it does very short and unnecessary pulses on the air intake/exhaust fans once the temperature setpoint is reached. Cooldown becomes slow below around 120C and very slow below 100C, although the in/out fans are running. Typically not an issue, just open the drawer and wait 30sec for the final cool down.
It is annoying though that the drawer does not have a latch. The air intake fan seems to be a bit stronger than the exhaust fan and seems to spin up faster. This is not an issue during cool down (where the fans start with a lot of short pulses before being powered continuously), but it is when starting a new process before the oven has cooled to the final temperature of the cool down step, which is also used as the starting temperature of the preheat step.
So upon process start, the actual temperature is much higher than the set point, so the fans start full speed. This pressurizes the oven and the drawer opens about one inch in my unit. I started to lay a hammer in front of the drawer as temporary fix . Would be nice if the process would just start at the current temperature to avoid the completely nonsensical fan spin for 30 secs or so. With the drawer not fully closed, the soldering results are bad because the front part of the oven will be colder.
The oven is not air tight, so it will blow out some warm/hot air. Flammable items should be kept at a distance, but my rubber desk top seems ok. But most of the solder fumes go through the exhaust, so all good there.
The controller shows the actual temperature curve, but updates a few pixels at a time, which is weird (maybe they don’t take a datapoint for every display pixel, but for a fixed time interval which is longer than one pixel duration in the plot). At the end of a process, the unit will beep and keep the fans spinning until stopped by the user.
It would be a nice feature if one could select to wait after each step until the temp. set point is reached before continuing with the next step, but thats not there.
Soldering results:
This is an IR oven with some convection added, but heating is still predominantly IR. I made some experiments and found that with the factory-supplied lead-free profile, green, red, and blue boards could be soldered just fine, although I had to add about 5 seconds to the reflow time to improve reliability with small inductors and such (228C target temp. for reflow).
Black PCBs were overheated, though - the silk screen became brownish - so I attached a TC to a bare board and measured 30C more than the oven indicated. So I had to set up a second profile for black PCBs with a lower reflow temperature (217C). With this profile, my black PCBs could be soldered fine without visible damage.
Because most of the heat is IR, there is shadowing. 0805 resistors right next to bigger parts (little transformer) were not soldered a few times. In addition: Don’t use the outer 5cm of the drawer, there are some cooler spots there (and more shadowing, in the center you are always ?between“ two IR heating rods), so I got some un-reflowed components when placing a board there. Two boards 10x15cm plus a narrow one next to them worked fine (i.e. at least 20x20cm homogeneous solder area).
I have added photos of my first boards with the oven. The solder paste is lead-free Henkel/Loctite GC10 SAC305T3 (Sn96.5Ag3Cu0.5), printed with a stainless stencil, hand placed.
Little transformers like Murata 78253/55JC are soldered fine (beware of shadowing though, had one un-reflowed joint in 10 boards with specifically that transformer), inductors like Fastron PIS2816 work fine, also uSD-sockets and 40x0.5mm FPC connectors for displays. Huge inductors like Murata 6000B series don’t seem to work at all (at least I didn’t want to fry all the other components by increasing the reflow time sufficiently), no surprise given their huge thermal mass.
Summary:
I would buy this oven again. Sure it would be nicer to have a perfect oven, but that would require a much higher budget which is not justified for me. It does what I need, and is definitely an improvement over hot-plate reflow soldering. The temperature controller is usable as is and the power good enough to do lead-free soldering of regular components, but not for huge inductors or caps. But this is for small scale soldering, so doing them by hand is ok (at least for me).
- Comments(1)
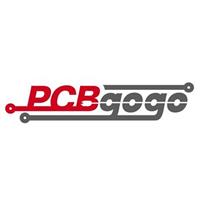
A****min
Sep 18.2019, 17:33:51
How about gluing two neodium magnets to the front sides of the drawer so when it is closed the magnets would hell keep it in place