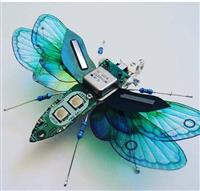
How should I decide on which footprint for chip capacitors to use? Should I create a separate footprint for caps from each manufacturer (and each of their dimensional tolerances)?
I have so little experience with commercial board assembly that I see a multitude of answers, which I've tried to outline below.
I'm having some expensive boards assembled (down to 0201 and 0.4mm PQFN pitches...., with "HDI" technology). I don't want them to be screwed up.
Do people normally use a footprint generator to calculate the pad sizes, or go by the manufacturer recommended footprints? Or should I ask the assembly company to tell me what pad sizes to use?
Or do people not normally worry about it, as they swap between brands of passives quite often, so there is no point designing for a particular model? Though, there are some like with epoxy terminals which are much more variable than the run-of-the-mill parts.
Using Murata 0402, 0.5mm height, using "nominal" dimensions as an example, I see that there are three separate tolerances for the lengths of the capacitor (1.0 +/- 0.05), (1.0 +/- 0.1) and (1.0+/-0.2). Plugging them into the "Library Expert Pro" utility, these generate three different footprint geometries. Which should I use? It seems I need to lookup each capacitor individually, and associate them manually? Or just use an average value for all 0402 size? Or use the loosest tolerance to insure that there is enough clearance between parts for assembly?
I mostly use Murata capacitors. I can download a table of their capacitors from their product search (with size tolerances), but only 1000 at a time. Is there a better way to bulk download the part numbers more than 1000 at a time, to import them into a component library (for Altium, sqlite database built from Python scripts)?
- Comments(1)
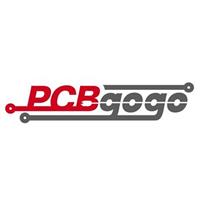
A****min
Mar 10.2020, 16:07:21
IPC calculated footprints are generally the place to be. The dimensions are most likely to suit all components compliant with the body dimensions, and more likely that CMs have tuned their process to those dimensions.
Regarding termination width: it's bullshit, and I suspect some don't even read the dimensions they put there, or derive the dimensions from their actual process. I think I've seen (but don't have an example handy unfortunately, so this is just hearsay) dimensions and tolerances that suggest the device can sometimes be shorted out from the factory (metallizations overlapping). But of course, a real part would never be /that/ bad.
Most of all, sanity-check the dimensions you're using, and review the footprint yourself. Preferably run an automated DFM check. Preferably purchase real parts ahead of time, and measure them yourself. Plan a small alpha build where you expect some things to go wrong, and fix "all" of them in the beta build. Etc.