
I am considering an experiment to make DIY PCBs. The goal/purpose of DIY is primarily to make fixtures for tests and assembly as well as working out various circuit designs that cannot be bread-boarded.
The technical needs are modest - double side, no mask, no silk. Not sure what minimum trace width I can get away with, but nothing crazy. With all that out of the way - I have reviewed all the usual DIY PCB methods out there (even made a few when I was a kid). They are all too time consuming and/or fiddly to be interesting until I considered the option of using my Epilog laser marking machine to replace the transparencies, toner transfer, exposure part of the process. The laser can go up to 1200dpi and have a dot circle of around .003" / .076mm.
I was thinking that I just buy pre-sensitized PCBs, put them in the laser, out of the laser into developer and etching. On paper, it sounds fast and easy but I may be naive about what it is really like. I saw a YT video where someone did a PCB in a similar way - looks like a good idea since I already have the high resolution laser system which is the majority of the cost.
Also, one of the goals is to be able to deal with the fact that the majority of my PCBs are not squares. If I am going to work out a prototype shape with connectors, wiring, hardware and full assembly testing before sending for fab - I would need a router to both cut the outline as well as drill the holes. Any recommends for a reasonable quality router with very high-speed spindle would be good. There are a ton of super cheap, super crappy/fiddly options out there. It would be nice to have a step-up from the bottom, but not a super amazing top-of-the-line model either. I did my best to 3D model everything including fasteners, but until I build a few with real parts, hardware, and wires - it was not known if it could be assembled. Tiny details matter and being able to quickly spit out 5-10 PCB shapes to optimize production assembly process would be a great time saver. Even the fastest PCB fab is a few days and at that speed it is top price of at least a few hundred per pass between the fab and overnight shipping. If I have 4-5 interconnecting designs, it could be significantly more money in addition to the time.
I may be crazy, but this seems cheap to try. Any tips from those that have done any of this would be great to hear.
- Comments(1)
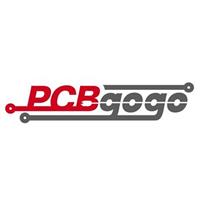
A****min
Dec 19.2019, 17:54:09
positive is very unforgiving - if you have a 10micrometer crack in your transparency then you'll end up with a 10um crack in the photoresist and even wider crack after etching because with positive you basically destroying the photoresist with UV, so any imperfection in the transparency will result in holes and cracks in traces. if you'll use direct imaging as you describe then it's the same - any reflected/scattered UV light form you UV source will damage the surrounding resist.
furthermore any level of overexposure means start over, with presintized boards it's a big waste.
another disadvantage of positive presintized is the developer solution - it's sodium hydroxide... 3% solution is developing the resist while more concentrated hydroxide is removing the resist
with negative method you're curing the photo resit so any imperfection in mask or scattered/reflected UV will just partially cure the surrounding resist - and you can easily compensate for that during developing the resist.. you simply keep it a bit longer in the developer solution (washing soda) and monitor it till the unwanted half-exposed artifacts are gone. the fully cured resist won't go anywhere it's rock solid so you can developing the board for ages . i saved once a significantly overexposed board (was lazy to laminate a new one - but would be faster to laminate a new resist) by developing it for something like 15-20 minutes
and if you really mess it up then just remove the resist with NaOH , clean and rinse the board, laminate a new resist onto it (with a standard unmodified office laminator) and repeat