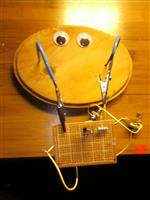
I have a board I've designed, and I feel it's nearly ready for me to get a small batch made. I'm aiming at using one of the cheap Chinese manufacturers. This will be the first time I've had some proper PCBs made, and I have a nagging doubt about whether I need to be concerned about my drill sizes.
The patterns/footprints for all the through-hole components I've been using have mostly been straight from my software's default library, without modification. And for a few other uncommon components, I've followed the exact dimensions the manufacturer recommends in their datasheet. As a result, I have a wide variety of through-hole diameters - 16 distinct sizes in all.
It is my understanding that most of these Chinese board manufacturers only use metric drill sizes, potentially ranged in 0.05mm increments (although that's a guess, as hardly any of them specifically state that info). I presume, if presented with a drill file with non-metric sizes, they perform some kind of 'normalisation' process to convert the hole sizes to match the metric tooling they have? Does anyone have insight into what they generally do? Would they just round the sizes up to the next 0.05mm increment?
- Comments(1)
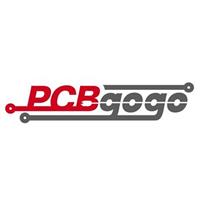
A****min
Jan 15.2020, 09:04:30
Real answer.... is yes and no
Any legitimate PCB (or anything else) manufacture will size to exactly what you specify.....to within the tolerance that is stated for work.
So if you specify a 1mm hole and the stated tolerance is +-0.05mm you will get a hole that is 0.95-1.05mm. The tool they pick is up to them, as long as it meets the specs, you specify 1mm hole, and for some reason they only have a 1.025mm dill, you will get a 1.025mm hole... but it's within spec so is fine.
When you specify 1mm hole, that is the nominal hole size (not actual), the actually hole size is the nominal+tolerance. They do 'normalize' (so yes), but should be within spec (so no).
When you go bargain without specified tolerances, then it's up in the air.