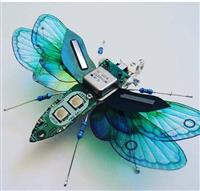
Anyone have any recommendations on how much clearance is required between the edge of a via hole and the edge of the soldermask for reliable tenting? Essentially I'm wondering how close to a pad I can put a tented via before having to worry about solder thieving. Obviously the design clearance will need to take into account the manufacturer's mask alignment tolerance, but once that's accounted for, how much clearance is required to ensure good adhesion of the mask? Is it sufficient to go by the manufacturer's minimum mask width?
- Comments(1)
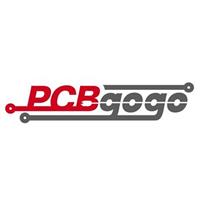
A****min
May 30.2019, 17:21:11
if the via is completely tented : the minimum annular ring + the minimum solder mask aperture.
they guarantee a drill strike on the via pad , but not necessarily on the center. so the annular ring protects them for off-center strikes.
worst case they strike so the drill edge touches the pad edge. ( if they go over the board is rejected )
in this case the registration offset of the mask is too tight and solder could leak in.
so by adding the minium solder mask aperture in such a case you still have the minimum solder mask aperture to protect you