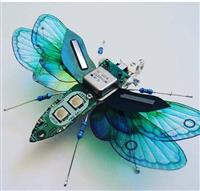
Hi, I have been doing prototype boards and small production runs for the last years and usually have very good results, but still struggle with 0.5mm QFP.
I use Loctite GC10 paste and reflow oven. Stencil are are stainless steel, both framed and non-framed. I have issues when placing parts by hand and also when using the PnP.
Way too many QFP need rework, I rarely encounter a single IC without a solder bridge.
For the boards I use 4mil solder mask expansion. In theory this should leave a 0.3mm solder mask strip between the pins. Hover looking at the bridging under the microscope shows the bridges are not necessarily at the end of the pins (where they touch the board) but often 'higher up' and closer to the IC. Too much paste?
I don't have the same problems with 0.5mm QFN..
Any suggestions to what I might try to optimize my process?
Thanks
- Comments(1)
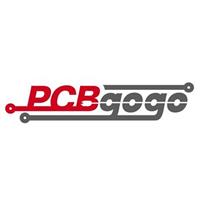
A****min
Feb 19.2020, 18:09:05
1.Use QFN instead. They are way less prone to bridge.
2. When QFP/TSSOP have to be used, design a longer solder pad. Say, if your pin is 0.25mm*0.75mm, design pad to be at least 0.5mm extended to the exterior side on all 4 sides. The extended part helps absorbing excessive solder. Do not extend in interior side (under the chip) as trapped solder tends to bridge and is very hard to wick away.