
I was trying to think of a way to come up with some sort of baseline measurement system for the time it takes for a household iron to bring the copper laminate up to a specific temperature while using the toner transfer method of making home rolled pcb's.
The idea that I came up with was to utilize the resistivity of copper and calculate the required change in the resistance of the laminate for a given temperature. At which point I could apply the iron and measure the amount of time it takes to reach the calculated resistance value. Effectively, this would be a variation on how one would typically evaluate the core temperatures of a transformer. This would be used as a one shot for a few different board sizes and the measurements would not be taken while actually attempting to transfer the image.
While it wouldn't be exact by any means, and it's intent is to come up with a quick and dirty reference value, I think it would be good enough to take a lot of the guesswork out of the process. The down sides that immediately come to mind are that you'd need to use the 4 wire method and a good bench meter to measure the VERY low resistances along with the need to have the probes fixed to the laminate during the heating process which may or may not damage them.
Has my cheese slipped off the proverbial cracker or does this seem reasonable?
Comments, suggestions?
- Comments(1)
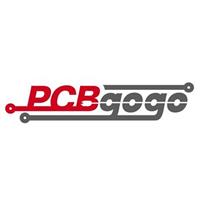
A****min
Feb 13.2020, 17:08:14
Thin insulated steel wire attached to the copper, and use the copper as the other wire in an iron copper thermocouple. simple, and accurate enough at this temperature. You will need a millivolt meter and a correction table along with the temperature of the meter to calculate the temperature. Otherwise find a display that will handle an iron copper thermocouple, or if you can get thin insulated nichrome wire use a copper nickel curve.