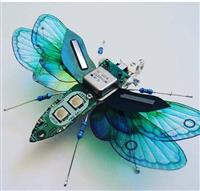
Hi
Last week I ordered a hot air station and a PCB pre-heater, in preparation for some PCBs I'll be soon be assembling.
The first job I had for them, though, was a trial by fire. I needed to replace a few SMT LEDs on an aluminium PCB.
The shiny underside of the board does a fine job of reflecting away the heat from the pre-heater, which needed to be turned right up to compensate. Even then, I wasn't able to get the board much above 115C (measured using a thermal camera) using the pre-heater alone.
Conversely, the aluminium also conducts away heat from the hot-air station, so raising the local temperature of the board to the point at which solder melts requires a great deal of extra heat.
But: the LEDs themselves are plastic, and melt at the slightest whiff of hot air.
The technique I settled on after a few failed attempts, was to set the pre-heater to 350C, and to hold the PCB in a vice as close to the heater as possible. I set the hot-air station to 450C and 65% of max air flow, and applied heat to either side of the LED. After a while, the board finally became hot enough to reflow the solder joints, and the LED became attached to the board without melting.
This worked fine until I tested the finished product. Unfortunately the solder paste I was using had softened with the heat, spread out into a puddle, and shorted the LED pins together underneath the device. I had to take them all off again.
What eventually worked, was to tin the PCB pads with a regular soldering iron (JBC CD-2D with T245-C handpiece), melt them all with hot air, then place the LED onto the pads while the solder was still liquid. This gave better control over the quantity of solder, and where it ended up. I had to touch up some joints with the iron afterwards, but the final result worked perfectly.
I'm hoping that when I start working on regular FR-4 boards, their relative lack of thermal conductivity will make for an easier job.
In the meantime, does anyone have any tips to share for working on aluminium PCBs and/or with very heat sensitive components?
- Comments(1)
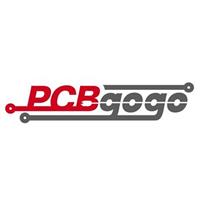
A****min
Oct 30.2019, 17:25:23
Get a proper reflow oven. Or build one.
Big advantage of oven is that it brings ALL parts and PCB to the same temperature, so there is no need to use much higher temperature air (and risk thermal damage of parts) in order to bring large copper pours up to the solder's melting point. You can even forego thermal reliefs if you don't intend to hand-solder parts, as reflow oven will bring everything to the reflow temperature. This also eliminates risks of any sort of cracks due to uneven heating, or damage from thermal shock - this is a big problem for small (0402) ceramic caps.