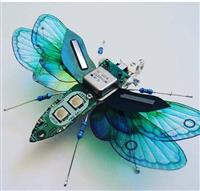
i all
I'm looking for the good practices to do PCB tinning to increase the current handling capability of traces on a power supply board.
My questions are:
- is there any table of the tinning width/thickness and the increased current handling?
- should the soldermask windows be aligned or perpendicular to the solder wave direction?
- is there a min/max/ideal width, should it cover the track completely or leave some soldermask on the edges?
- what about tinning ground planes to increase thermal?
For example:
- Comments(1)
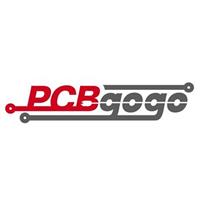
A****min
Nov 15.2019, 18:16:55
one of the points made is that solder - even silver solder - has about 6x to 9x higher resistivity than copper, so any improvement in total ampacity of a trace from HASL/tinning will be minimal.
If you really need higher ampacity for a given trace width then choose thicker copper plating for the board (e.g. - 2oz/0.07mm or 4oz/0.14mm). Same if you need better thermal conductivity.