
Hello,
I've got a question about manufacturing boards with a high-enough Comparative Tracking Index (CTI) and solder mask applied. I think I've got an understanding on the subject, but since I basically lack both the experience and material/chemical knowledge, I would like to ask people here. Thank you for your help.
Let's assume I have a PCB with solder mask (in order to get an understanding of how manufacturing for CTI works, please don't ask if the solder mask is required). Let's also say that the PCB's FR4 laminate is made of high-CTI material. The question: If the solder mask is only normal/low CTI, will it reduce the CTI-rating of the finished board?
My understanding is that CTI (although it also depends on the material thickness) is primarily a surface material property. That is, a low-CTI coating applied to a high-CTI base will not have the same high-CTI performance as the base material itself. Also, given a high-CTI coating, due to the dependence on material thickness, to get the high-CTI rating for the whole product, the coating either 1) needs to have a high enough thickness, or 2) the base material will also need to be high-CTI. That is, it is possible to have a high-CTI product if only the solder mask is high-CTI (depending on the mask's properties), but it is never enough to make only the base laminate high-CTI but not the solder mask (assuming that there is a solder mask at all). Is my understanding correct on these?
Thanks for helping me getting a grip on the subject.
- Comments(1)
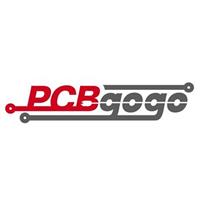
A****min
Dec 30.2019, 17:37:57
It's just that CTI is also used as a figure of merit for an insulator.
How an insulator endures voltage stress through a PCB laminate, due to traces on either side or on inner layers, is just as important to safety and is also why high CTI is specified.
OP, by your reasoning you could use low CTI PCB laminate with low CTI soldermask- but apply a conformal-coating with high CTI rating and have no issues.
If you really want to understand how to bypass the safety standards, look at the parent IEC 60664-1 (bold added by me)
4.8 Insulating material, 4.8.1 Comparative tracking index (CTI)
4.8.1.1
Behaviour of insulating material in the presence of scintillations
With regard to tracking, an insulating material can be roughly characterized according to the damage it suffers from the concentrated release of energy during scintillations when a surface leakage current is interrupted due to the drying-out of the contaminated surface. The following behaviour of an insulating material in the presence of scintillations can occur:
– no decomposition of the insulating material;
– the wearing away of insulating material by the action of electrical discharges (electrical erosion);
– the progressive formation of conductive paths which are produced on the surface of insulating material due to the combined effects of electric stress and electrolytically conductive contamination on the surface (tracking).
NOTE Tracking or erosion will occur when
– a liquid film carrying the surface leakage current breaks, and
– the applied voltage is sufficient to break down the small gap formed when the film breaks, and
– the current is above a limiting value which is necessary to provide sufficient energy locally to thermally decompose the insulating material beneath the film. Deterioration increases with the time for which the current flows.
4.8.1.2
CTI values to categorize insulating materials
A method of classification for insulating materials according to 4.8.1.1 does not exist. The behaviour of the insulating material under various contaminant and voltages is extremely complex. Under these conditions, many materials may exhibit two or even all three of the characteristics stated. A direct correlation with the material groups of 4.8.1.3 is not practical.
However, it has been found by experience and tests that insulating materials having a higher relative performance also have approximately the same relative ranking according to the comparative tracking index (CTI). Therefore, this standard uses the CTI values to categorize insulating materials. "