
We're having some trouble with yield on a consumer product that incorporates one of ST's accelerometer chips. We're failing up to 40% of our assembled boards during testing because the accelerometer readings are out of spec. The test methodology is basically looking for offset along each of the X, Y, and Z axes... and our error bands are actually larger than what the OEM recommends. If we used their guidelines, we'd have an even lower yield.
These failures a specific to the accel chip in that we can take a failing board, replace the accel by hand, and it'll be perfect. If we take an accel chip from a failing board and reflow it onto a previously working PCB, the failure moves with the bad part.
We have two hypotheses: 1) some kind of SMT issue is causing stress on the accel package which causes these offsets. 2) Ham-handed depanelization at the CM. Our panels use mouse bites (not fully routed) and individual boards are snapped out using a jig. Perhaps the snapping process causes too much shock and damages some of the MEMS chips.
Maybe 3) would be a bad reel of parts from ST, but I find that really hard to believe.
Does anyone have experience with this kind of problem? How would you go about finding the root cause?
- Comments(1)
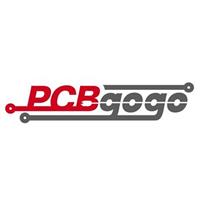
A****min
May 25.2019, 10:13:35
The way of breaking the panels could be a real problem - when breaking things apart, one can get really high amplitude vibrations, that can break things, sometimes even less sensitive parts than MEMs devices, like capacitors or inductors in an unfavorable position.