
I have a relatively simple product that is a single 10x10 cm PCB in a metal enclosure, and currently the quality control just consists of functional tests and visual inspection of the board. I have only sold less than 100 units but already saw 2 defects in the field. The units were all tested prior to shipping and arrived defective at the customer, so the damage is due to bad solder joints.
Is shock & vibration testing every unit typically the solution or do most manufacturers rely on AOI/visual inspection?
- Comments(1)
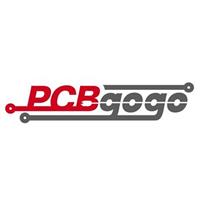
A****min
Sep 27.2019, 18:10:21
Please be specific. - Bad reflow, wave or hand-soldering joints? Please tell more about those 2 defects. What you mean by saying "units were all tested prior to shipping"? Manufacturers usually rely on 1) PCB houses with AOI capabilities 2) thermal cycling (environmental) chambers and/or 3) burn-in. Vibration tests are not common unless you manufacture specific product for harsh environment. For usual electronics you do vibration tests only on prototypes and maybe first batch to reveal mechanical/PCB_layout/packaging engineering errors.
In short: consider thermal chamber. Cycle count and time proportional to product price. Usually you cycle through whole specified temperature range at least two cycles, each cycle ~1 hour or so. If have spare time - run as many cycles as your manufacturing specifics allows.