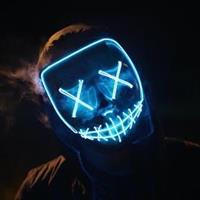
Raw materials in this article refer to the basic raw materials on PCB (printed circuit boards) manufacturing process, which can also be called PCB substrate materials. From the beginning of the 20th century till the end of the 1940s, the PCB substrate material industry started to sprout. Because resins, reinforcing materials, and insulating substrates for substrate materials emerged in large numbers during this period, the technology was initially explored.
These have created the necessary conditions for the birth of the most typical substrate material for printed circuit boards - CCL (copper-clad laminates). Additionally, the PCB manufacturing technology called etching has been initially established and developed, which plays a decisive role in the determination of the structural composition and characteristic conditions of the CCL.
The PCB substrate material industry has a history of nearly a hundred years. Not only the raw materials of printed circuit boards have been iterated for nearly 50 years, but also there are 50 years of scientific experiments and explorations on the basic raw materials used in this industry - resin and reinforcing materials. Each stage of the substrate material industry is driven by innovation in semiconductor manufacturing technology, electronic installation technology, and PCB manufacturing technology.
INTRODUCTION OF PCB RAW MATERIALS AND PARAMETERS
1. Classification of CCL
Copper Clad Laminate, abbreviated to CCL, is a type of base material of PCBs.
1. 1 The first classification of CCL can be seen from the varied reinforcing materials, which are usually paper, glass fiber, composite material(CEM series), laminated multi-layer board, and other special materials like ceramic, metal core base, etc.
1. 2 The second classification refers to the different resin adhesives used in the PCB.
Phenol resin (XPc, XxxPC, FR-1, FR-2, etc.), epoxy resin (FE-3), polyester resin, and other types are typical materials for paper-based CCL.
For the common glass fiber cloth base CCL, they have epoxy resin (FR-4, FR-5), which is the most widely used glass fiber cloth base type.
1. 3 The third classification is to refers to flame retardant properties of CCL, it can be divided into flame retardant (UL94-VO, UL94-V1 grade) and non-flame retardant (UL94-HB grade).
1.4 Knowledge of CCL - Environmentally-friendly flame-retardant CCL is a new form of CCL that doesn't include bromine. CCL's performance standards have risen in tandem with the fast advancement of electronic technology. There are three types of CCL and were distinguished by the performance: general performance CCL, low dielectric constant CCL, and high resistance. The most generally used type of CCCL is glass fiber cloth basis nowadays.
2. Main Criteria for Substrate Materials
National standards: The GB/T4721-47221992 and GB4723-4725-1992 are Chinese national standards for substrate materials. The CNS standard, which was introduced in 1983 and is based on the Japanese JIS standard, is the copper-clad laminate standard in Taiwan.
International standards include the Japanese JIS standard, the American ASTM, NEMA, MIL, IPC, ANSI, UL standard, the British Bs standard, the German DIN, VDE standard, the French NFC, UTE standard, the Canadian CSA standard, the Australian AS standard, and the former Soviet Union FOCT standard, etc. Suppliers of PCB design materials include Shengyi/Jiantao/International, etc.
3. Parameters of Substrate Materials
Accepted documents: Protel/AutoCAD/PowerPCB/OrCAD Gerber, etc.
Type of sheet: CEM-1, CEM-3 FR4, high TG material;
Maximum board size: 600mm*700mm(24000mil*27500mil)
Processing board thickness: 0.4mm-4.0mm (15.75mil-157.5mil)
The highest number of processing layers: 16Layers
Copper foil layer thickness: 0.5-4.0(oz)
Finished plate thickness tolerance: +/-0.1mm(4mil)
Forming size tolerance: Computer milling: 0.15mm (6mil) Die punching plate: 0.10mm (4mil)
Minimum line width/spacing: 0.1mm(4mil) Line width control ability: <+-20%
Finished minimum drilling hole diameter: 0.25mm (10mil)
Finished minimum punching hole diameter: 0.9mm (35mil)
Finished Aperture Tolerance: PTH: +-0.075mm (3mil)
NPTH: +-0.05mm(2mil)
Finished hole wall copper thickness: 18-25um (0.71-0.99mil)
Minimum SMT chip pitch: 0.15mm (6mil)
Surface coating: chemical immersion gold, tin spraying, nickel gold plating (water/soft gold), silkscreen blue glue, etc.
Solder mask thickness on board: 10-30μm (0.4-1.2mil)
Peel Strength: 1.5N/mm (59N/mil)
Solder mask hardness: >5H
Solder Mask Capability: 0.3-0.8mm(12mil-30mil)
Dielectric constant: ε= 2.1-10.0
Insulation resistance: 10KΩ-20MΩ
Characteristic impedance: 60 ohm±10%
Thermal shock: 288℃, 10 sec
Finished board warpage: < 0.7%
Applications include communication equipment, vehicle electronics, instrumentation, global positioning systems, computers, MP4 players, power supplies, and domestic appliances, among others.
4. The Classification of PCB Substrate Materials
PCB substrate materials can be divided into paper-based printed boards, epoxy glass fiber cloth printed boards, composite substrate printed boards, special substrate printed boards, and other substrate materials according to the properties of the materials.
EXPLANATION OF TERMS
1. Paper-based PCB
This type of printed board is made of fiber paper as a reinforcing material, dipped in resin solution (phenolic resin, epoxy resin, etc.) and dried, covered with glued electrolytic copper foil, and pressed at high temperature and high pressure. According to the models specified by the American ASTM/NEMA standard, the main varieties are FR-1, FR-2, FR-3 (the above are flame retardant XPC, XXXPC (the above are non-flame retardant). 85% of global paper-based PCBs The above markets are in Asia. The most commonly used and mass-produced are FR-1 and XPC PCB
2. Epoxy Glass Fiber Cloth PCB
This type of PCB is a substrate using epoxy or modified epoxy resin as an adhesive, and glass fiber cloth as a reinforcing material. It is the PCB with the largest output in the world and the most used type of PCB. In the ASTM/NEMA standard, epoxy fiberglass cloth board has four types: G10 (non-flame retardant), FR-4 (flame retardant); G11 (retains thermal strength, not flame retardant), FR-5 (retains heat strength, flame retardant). Non-flame retardant products are decreasing year by year, and FR-4 accounts for the vast majority.
3. Composite Substrate PCB
It is a substrate that uses different reinforced materials to form the face and core material. The CCL substrates used are mainly CEM series, of which CEM-1 and CEM-3 are the most representative.
CEM-1: base material is glass fiber, the core material is paper, the resin is epoxy, flame retardant; CEM-3 PCB is a composite copper-clad laminate.
FR-4 is made of copper foil and glass fiber cloth impregnated with flame-retardant epoxy resin. The difference between CEM-3 and FR-4 is that it is made of glass cloth and glass mat composite substrate. Also called composite. Not just glass cloth.
Metal substrates (aluminum-based, copper-based, iron-based, or Invar steel), ceramic substrates, can be made into metal (ceramic)-based single, double, multi-layer printed boards or metal core PCBs according to their characteristics and uses.
HOW TO PROCEED YOUR PCB DESIGN?
It's not always straightforward to choose the correct substrate and laminate for a PCB application. There's a delicate balance between quality and cost efficiency when it comes to high density, high frequency, or microwave frequency. By partnering with certain PCB manufacturers, you can avoid getting your wires twisted while lowering PCB assembly costs and lead times.