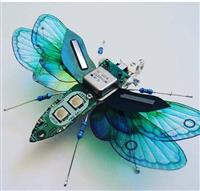
So what do you need for this more advanced process?
1) what method can be used to drill the hole? I understand they use a carbide drill with a excess of 100k rpm in an air spindle. Can you drill a hole conventionally and use something like a microreamer to clean it up? An option here would be to make a custom drill press that uses an air spindle so the hole can be drilled correctly.
2) how is the chemical process done? I assume you need something like a rocker table or a combined ultrasonic process?
I know its hard and not economical. I wanted something better then the copperset via kit.
If you have alot of time, can you electrodeposit a lip around the hole then use a micrometer connected to an annode thats being gradually removed to grow a verticle layer downards then do lapping to clean it up?
In the ink method is there significant adhesion between the electroplate and the via wall?
Then when you grow a almost full shorted cylinder, use a micropipet to inject liquidy epoxy around the via growth pcb hole interface as its cooled to make a verticle wall bond then finish the plating? There is significant differential contraction so a copper tube grown along side a fiberglass wall should shrink and allow thin glue to enter under vacuum.
I dont like the ink idea for some reason
- Comments(1)
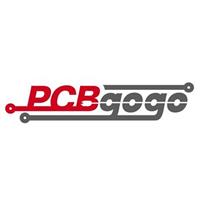
A****min
Sep 11.2019, 09:25:56
For drilling i would recommend standardising on one size of via hole and using a drill bit of that size in a CNC machine. Import the NC drill file into FlatCam and export gcode to the CNC.
For all other holes (i.e. anything larger than your standard via, like power connector leads) use a 0.8mm end-mill. After importing the NC drill file into FlatCam, select all the remaining holes and use the end-mill for those. FlatCam does the rest and generates gcode for the CNC.
I've found that the cheap store 0.8mm end mills are strong enough for most FR4 laminates I've tried them with. They are also cheap enough to keep a good stock of. I also tried 0.5mm end mills but with many breakages.